
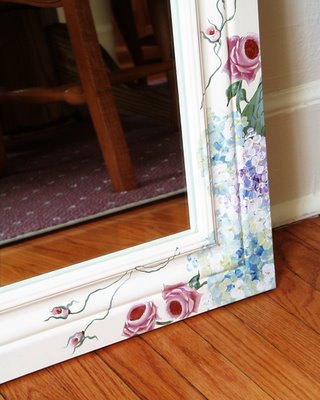
This week I had a customer contact me who was interested in having a custom mirror built and painted for her. She was very curious about the process that goes into these large, custom pieces so I thought this would be a great topic to blog about.
This particular mirror is 36" x 30" and was done with my Lush Hydrangea & Roses design. First, when someone contacts me about a mirror, we talk about the overall size, including the frame that they will be needing. Once a size and design are worked out, I go shopping at the home improvement store for moulding pieces that are large enough. My husband cuts them to the appropriate size and angle with his table saw and then uses wood glue and furniture nails to attach everything together. The corner angles have to be cut correctly and fit together just right or the mirror frame will be a mess.
At this point, I come into it and prep the wood for paint, I do this by using an all purpose wood sealer that I sponge on. Then my least favorite part....I get to sand the whole mirror frame, front , back, sides and the nooks and crannies. I vacuum the frame quite well after this step and will also clean the surface with a clean moist cloth. I then paint on several coats of a background color (whatever the customer decides on) with a large sponge. When this is dry, I'm ready to paint my design. Depending on what kind of a design I'm doing, this takes quite a few steps to complete thoroughly. The bad part about being a perfectionist is that you keep looking at things, even after you have supposedly finished them, constantly tweaking and adding/changing things.
About this time, I custom order the mirror from a local glass shop that I work with on a regular basis. My husband Chris does all the measurements so it will fit just right into the opening allotted. I then seal the frame with a protective finish which I sponge one. All areas get several coats and when I'm finished with it, the mirror can happily live anywhere in the house it wants. Lots of these mirrors are purchased for bathrooms so, they can withstand the steam and humidity thanks to the protective finish.
At this point I hand the mirror frame back over to Chris and he attaches the mirror in the back. He then papers the back for a professional finish and adds a heavy duty guage wire for hanging.
Then the mirror needs to get ready for its trip anywhere in the country or the world for that matter. Chris builds a wooden crate for the mirror and every inch is padded with foam and paper on the inside to protect it on its journey.
So there it is, if you have ever wondered what went into a custom mirror, this is it in a nut shell.
No comments:
Post a Comment